Reactive Electron Treatment of Polymers
![[Translate to English:] Header](/fileadmin/HTW/Fakultaeten/LUC/Bilder/Forschung/Chemie/Elektronenbehandlung/electrontreatment_header.jpg)
Accelerated electrons are used in various thermal and non-thermal applications for the temporally and spatially precise energy input into materials. In contrast to thermal applications (heat treatment, melting, welding, vapour deposition, nanostructuring), non-thermal electron treatment aims to modify material properties through the spatially and temporally precise generation of chemically reactive species.
Accelerated Electrons Transfer Energy and Charge
After leaving the vacuum, the accelerated electrons hit the plastics/products to be modified. The treatment depth of the electrons is controlled by the electron energy. The energy absorbed per mass (dose) characterises the intensity of the electron treatment. The interaction of accelerated electrons with matter is subject to a time sequence and can be categorised into the physical, physical-chemical or chemical phase.
Cleavage of Covalent Bonds/ Formation of Polymer Radicals
The physical phase comprises the energy and charge transfer of accelerated electrons. The physico-chemical phase ends with the formation of polymer radicals.
Cleavage of Existing C-C Bonds/ Formation of New C-C Bonds
In the chemical phase, the polymer radicals initiate various chemical reactions that can lead, for example, to the cleavage of existing C-C bonds (polymer degradation) or to the formation of new C-C bonds (polymer formation). The chemical reactions depend on the properties of the polymer material, can be controlled via process engineering parameters during and after electron treatment and can be categorised as follows:
Polypropylene and polylactides tend to preferentially cleave C-C bonds after electron treatment in air at room temperature. Polymer degradation is often associated with oxidation and yellowing. Typical applications are:
- Selective adjustment of the melt mass flow rate of a thermoplastic for compounding, injection moulding and extrusion.
- Production of polytetrafluoroethylene micropowder
- Polymer degradation of cellulose for the production of viscose
- Sterilisation of medical devices
Grafting describes radical reactions with monomers containing double bonds and is used for targeted surface or volume functionalisation. The framework polymers are activated, for example, by means of accelerated electrons. The subsequent graft copolymerisation leads to the application-specific functionalisation of the scaffold polymer. Applications are:
- Production of proton exchange membranes for fuel cells and vanadium redox flow batteries.
- Production of separators for lithium secondary batteries
Curing characterises the polymer radical-induced polymerisation and cross-linking of oligomers containing double bonds. A strongly cross-linked non-swellable duromer is formed. Typical applications are:
- Curing of carbon fibre reinforced reactive resins (fibre composites).
- Curing of paints and coatings on various substrates
- Production of pressure-sensitive adhesives
Cross-linking is based on the recombination of polymer radicals. A non-melt-flowable polymer is formed. Typical applications are:
- Cross-linking of single and multi-layer pipes as well as cable insulation.
- Production of shrink products and shape memory polymers
- Production of foam products with closed cells
- Partial cross-linking of tyre components
- Production of hydrogels
- Production of high temperature resistant SiC fibres
Cooperation Partners
- Prof. Dr. Sabine Beuermann, Clausthal University of Technology, Institute of Technical Chemistry, Arnold-Sommerfeld-Strasse 4, D-38678 Clausthal-Zellerfeld, Germany
- Prof. Dr. Dan Xiao, Fujian University of Technology (FJUT), School of Materials Science and Engineering, No. 3 Xueyuan Road, 350118, Minhou, Fuzhou, China, https://www2.fjut.edu.cn/2017/0924/c5272a70507/page.psp
- Dr. L. Mèszàros, Budapest University of Technology and Economics, Hungary, www.pt.bme.hu
- Dr. M. D. Stelescu, National R&D Institute for Textiles and Leather, Romania, www.incdtp.ro
- Dr. P. Rytlewski, Kazimierz Wielki University, Materials Engineering Department, Chodkiewicza 30 St, 85-064 Bydgoszcz, Poland, https://www.ukw.edu.pl
- PhD eng. D. Constantinescu, S.C. Monofil S.R.L., Romania, http://www.monofil.ro/
- Dr. K. Lauer, CiS Forschungsinstitut für Mikrosensorik GmbH, Konrad-Zuse-Str. 14, 99099 Erfurt, Germany, https://www.cismst.de
- Dipl.-Ing. P. Janßen, MTH Metall-Technik Halsbrücke GmbH & Co. KG, Ladestrasse 3, 09633 Halsbrücke, Germany, www.mth-kg.de
Contact
Head of Working Group
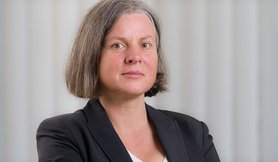
Research Associates
M.Sc. Aglaia Angolini
- A 206
- +49 351 462 2131
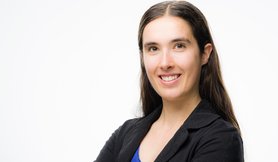
M.Sc. Katharina Knez
- A 206
- +49 351 462 2160
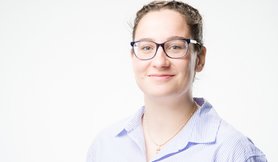
M.Sc. Annabelle Lindau
- A 206
- +49 351 462 2273
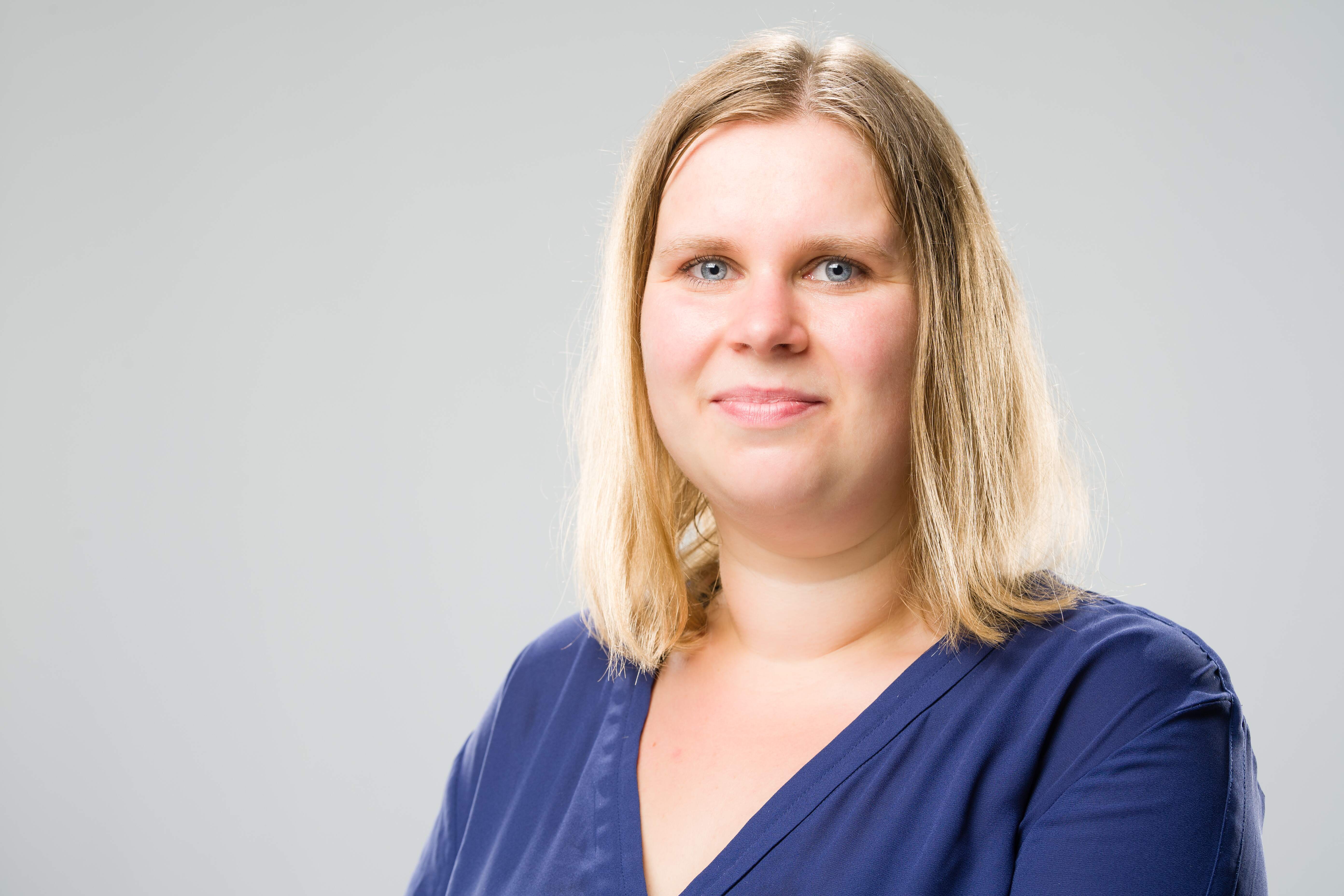
M.Sc. Yue Qi
- A 519
- +49 351 462 2097
